In the past, macroscopic Engineered Living Materials (or ELMs) would be produced using a top-down approach, that is, one would take a pre-existing macroscopic structure, and work to incorporate ELMs into that structure such that a biomolecular matrix forms. Alternatively, macroscopic ELMs have been grown on their own, but only by genetically modifying pre-existing matrix-forming microbes. In both cases, the finished productsâ composition, mechanical, properties, and potential for catalysis are dependent on that of the pre-existing entity being modified.
The motivation behind creating ELMs is the ability to create materials tailored for desirable functions. Thus, if they are to be used to their full potential, new strategies are necessary to address the material characteristics that as of right now show minimal variability. Enter âa de novo matrix for macroscopic living materials from bacteriaâ. âDe Novo translates to âfrom the beginningâ alluding to the researchersâ new procedures which begin ELM development at the genetic, and therefore nanometer scale, in an organism that does not produce its own extracellular structure and follow all the way through to the formation of a material measurable in centimeters.
Using prior engineering of the bacterial species Caulobacter crescentus which increased the bacteriaâs capability for surface-layer protein density, researchers designed cells that secreted a protein which interacted with other copies of itself to form a densely packed extracellular matrix. To do so, a gene encoding the protein which attaches to the surface layer of C. crescentus was replaced with functional coding regions that anchored the expressed protein to the surface in higher densities, influenced the material properties of the matrix, and allowed for secretion from the cell and interaction with other copies. A sequence known as SpyTag was also included which helped the researchers identify the proteinâs location and functionality. This gene was first added to an integration plasmid which was inserted into E. coli cells capable of conjugating the gene directly into the C. crescentus genome. From there, the protein, referred to as BUD for Bottom Up De novo, could be expressed as C. crescentus cultures were grown in liquid media where the BUD-based Engineered Living Material grew from the microscopic cells in culture, into a pellicle, a biological material several centimeters long.
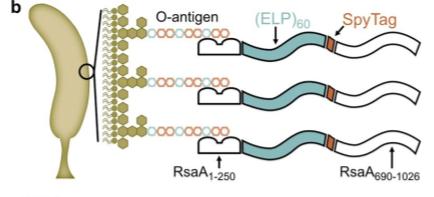
The process of growing these BUD-ELMs helped to identify the physical parameters necessary for effective ELM growth. The researchers varied the levels of oxygen that entered the medium through the liquidâs surface, the energy used to shake the medium during growth, and the diameter of the growth medium and discovered all three to have ranges which optimized BUD-ELM production to ensure the formation of a single pellicle. Deviating from these ranges resulted in the fragmentation of the BUD-ELM. The fully formed material could be imaged with several types of microscopy which showed a structure differing from wild-type C. crescentus which mediated interactions between cells, and the physical variations between differently edited strains of the BUD protein. Furthermore, taking advantage of a fluorescent protein able to bind to the SpyTag, and immunoblotting analysis which detects protein outside of the cell, imaging found that the matrix was made of proteins both attached and detached from the cell surface and was completely absent of lysed cells.
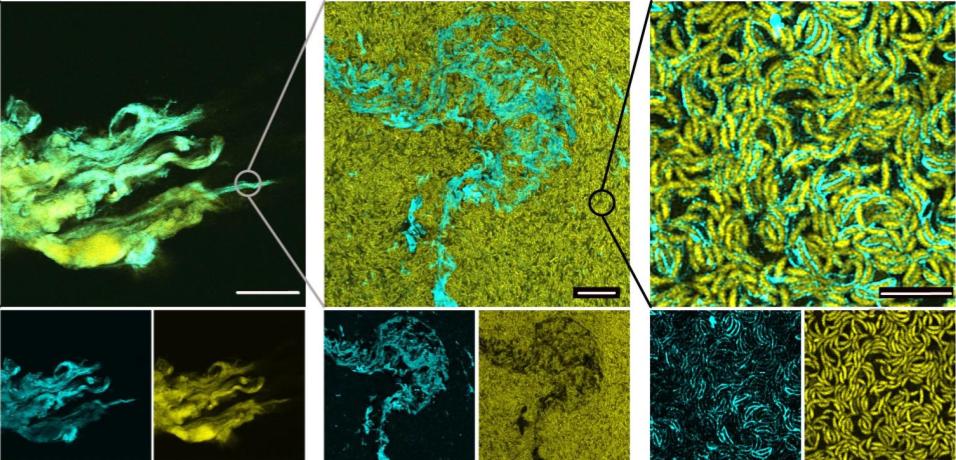
The functional regions encoding the BUD protein were designed with the particular intention of forming a high-density, surface-bound, elastic-like matrix; alterations to these regions during the construction of the integration plasmid proved how the resulting physical properties of the ELM could be altered. Removal of the surface-binding region of the protein developed a material shown to contain fewer cells when imaged, which is also more elastic, whereas removal of the group responsible for the elasticity creates a stiffer final material. The researchers also tested the regrowth ability, and functional capacities of BUD-ELM, finding it would fully regenerate after drying and 14 days of storage, remove heavy metals from water, and catalyze reactions when fuzed with other enzymes. Furthermore, BUD-ELM acted as a cementing agent when mixed with glass powder, and a cohesive paste when mixed with other cultured pellicles. These results support the great magnitude of the potential of ELM applications.
This degree of intervention in BUD-ELM development allows for a wider array of customizability of the resulting material. Not only is this new type of ELM proven to have versatile functional purposes, but its development has been empirically constructed to a degree reminiscent of the steps in a cookbook recipe. This discovery could represent the forming of a new branch of material engineering.